What is Cement?
“Cement” is a material with adhesive and cohesive properties that makes it capable of bonding mineral fragment into a compact and rigid mass. The word cement seems to have been derived from the middle age English “cyment”, and Latin “caementum”. The latter word “ caementum “ meant rough quarried stone or chips of marble from which a kind of mortar was made more than 2000 years ago in Italy. During the Middle Ages term “cement” or “sement” generally was made for a mortar. Common lime, hydraulic lime, gypsum plaster, “pozzolana”, natural and Portland cement are few of the material, which are used for cementing purposes. These cementing material may be classified into two groups:
Non-Hydraulic:
Non-hydraulic cement do not have the ability to set and harden under water but requires carbon dioxide from air to harden e.g. non-hydraulic lime and plaster of Paris. Their cementing prosperity arises from the re absorption of gases that were expelled during their processing. Their products of hydration are not resistant to water.
Hydraulic:
Hydraulic cement is defined as cement having the ability to set and develop strength in air or under water and which are insoluble in water after they have set. Such cement harden even in the absence of air and form a solid product which is stable in water and can be safely used in all structures in contact with water. Hydraulic cement includes hydraulic limes, Portland cement (both basic and blended), oil-well cement, white cement, colored cement, high alumna cement, expensive cement regulated and hydrophobic cement etc.
Quarrying and crushing
The primary raw material for cement manufacture is calcium carbonate or limestone. This is obtained from the quarry where, after the removal of overburden, the rock is blasted, loaded into trucks and transported to the crusher. A multistage crushing process reduces the rock to stone less than 25 mm in diameter. Most modern cement factories are located close to a source of limestone as about 1.5 tons of limestone is needed to produce one ton of cement.
Blending and storage
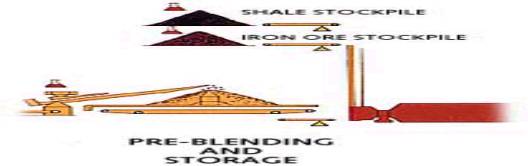
Raw milling and homogenization
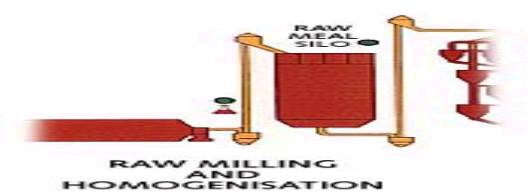
Carefully measured quantities of the various raw materials are fed, via raw mill feed silos, to mills where steel balls grind the material to a fine powder called raw meal. Homogenizing silos are used to store the meal where it is mixed thoroughly to ensure that the kiln feed is uniform, a prerequisite for the efficient functioning of the kiln and for good quality clinker.
Burning
The most critical step in the manufacturing process takes place in the huge rotary kilns. Raw meal is fed into one end of the kiln, either directly or via a preheater system, and pulverized coal is burnt at the other end. The raw meal slowly cascades down the inclined kiln towards the heat and reaches a temperature of about 1 450 °C in the burning zone where a process called clinkering occurs. The nodules of clinker drop into coolers and are taken away by conveyors to the clinker storage silos. The gas leaving the kiln is cleaned by electrostatic precipitators prior to discharge into the atmosphere.
Cement milling
The cement mills use steel balls of various sizes to grind the clinker, along with a small quantity of gypsum to a fine powder, which is then called cement. Without gypsum, cement would flash set when water is added and gypsum is therefore required to control setting times. The finished cement is stored in silos where further blending ensures consistency.
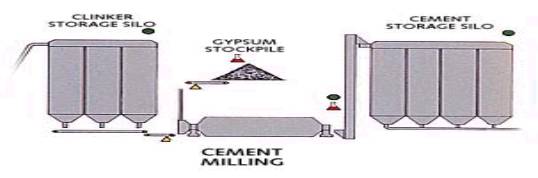
Quality assurance
Extensive sampling and testing during the manufacturing process ensures the consistency and quality of the end product. Testing takes place at the stages of the manufacturing process indicated by the symbol.
Cement despatch
Cement is despatched either in bulk or packed in 50 kg bags and distributed from the factory in rail trucks or road vehicles. The 50kg bags are either packed directly onto trucks or can be palletised. The pallets can be covered by a layer of plastic to offer further protection from the elements.
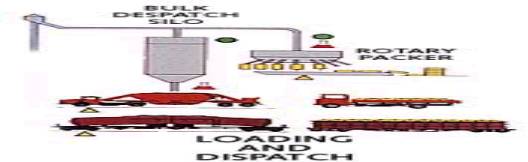
Types Of Cement:
The types of special cement now being produced can be roughly classified in the following six categories according to the special purpose for which these have been designed. These are:
- Rapid hardening cement.
- Cement resistant to chemical attack of certain soil and aggregates.
- Low heat of hydration cement.
- Better protecting cement for steel reinforcement.
- Better workability and whether resisting cement.
- Decorative cement and other special cement.
Rapid Hardening Cement:
Under this category following two cement have the desired properties of fast development of strength viz. the Portland Rapid Hardening Cement and High Aluminum Cement. “Their specific characteristics are as follows:
Rapid Hardening Cement (Type III of A.S.T.M):
This cement has high early strength, its equal to or better than 3 Days’ strength of OPC. This is achieved by having high contents of tricalcium silicates in its composition. It is mostly used in intended to release the framework within 24 hours or so for subsequent use in the mass production of RCC elements.
The respective 1,2,3,7 and 28 days’ strengths (in equivalent P.S.I figures) of this cement under British specifications, German standard, and A.S.T.M. Japanese and Pakistan standards for mortar cubes are as follows:
|
B.S.
|
German Standard
|
Astm
|
Japanese
|
Pakistan
|
1 day strength
|
-
|
-
|
1800
|
923
|
-
|
2 days strength
|
-
|
4350
|
-
|
-
|
-
|
3 days strength
|
4200
|
-
|
3500
|
1846
|
4205
|
7 days strength
|
-
|
-
|
-
|
3266
|
5220
|
28 days strength
|
6670
|
7975
|
-
|
4686
|
6670
|
The difference in strengths given above is basically due to difference in all standards the 3 days strength is nearly 1-1/2 to 2 times of O.P.C. The disadvantages of this cement beside its higher cost are its high heat of hydration, which renders it unsuitable for mass concreting projects.
High Aluminum Structural Cement:
This cement is used where very rapid setting and very high early strength are required. This cement has strength at one day nearly equal to 28 days strength of O.P.C. Its setting is so fast that it must be put in place within a few minutes of its mixing. It is generally used in plugging leakage in dams etc. or putting in pile foundations where limited time is available for setting of cement before the seepage water build up occurs. In Pakistan it has been used in some specific locations in terbela dam. Abroad it has been used in buildings where it was found essential to remove the framework after one or two days.
This cement besides its high cost has the disadvantages of the high heat of hydration and retrogression in strength in time. There have been some structural failures due to miscalculation of its final strength after some years of use especially in humid and hot atmosphere. This cement has however excellent heat registering qualities and is therefore extensively used in Kilns, boilers and Furnace linengings. Cement resistant to chemical attack especially of Sulphate and Organic acids or Soil and active Silica of aggregate. In this category the following cement can be included:
2-A Highly Sulphate Resistant Cement
2-B Moderately Sulphate Resisting Cement
2-C Portland Blast France Slag Cement.
2-D pozzolana Cement
2-E Low Alkali Cement
2-A Highly Sulphate Resisting Cement H.F.R.C
The most important and the most widely used chemical resistant cement is H.S.R.C cement High concentration of sulphate salts is present in seawater and in the soil near seashores. These salts are sometimes present in soil and in the submit water even thousands of miles away from the sea. Even Terbela Dam site was found not free from sulphate and H.S.R.C had to be used in foundations at the site. The sulphate salt severally attack concrete can start within months. This cement has lower 3 days strength than OPC and also its capacity to protect reinforcement steel in structures exposed to atmosphere action is lower than OPC and hence not recommended for usual R.C.C. work in super structures.
2-B Moderately Sulphate Resisting Cement (M.S.R.C.)
This cement has been developed as a compromise Cement having the good properties of sulphate resistance to some extent and of good alkalinity like that of OPC which useful for reinforcement protection and also of early strength development better than Highly Sulphate Resisting Cement. No standard exists for this cement in the B.S and P.S. specifications but under ASTM it is designed as Type II. The three days minimum strength of OPC, H.S.R.C & H.S.R.C is 1800, 1200 and 1500 PSI respectively under ASTM.
This cement though better than H.S.R.C in many respects is not as resistant to sulphate as H.S.R.C and should not be used in foundations near the seashore. Incidentally the O. P. cement produced in most of the Cement Factories around Karachi are confirming to the ASTM specifications for this type II and hence more resistant to mild sulphate attack than the cement produced in the factories in other parts of country.
2-C Portland Blast Furnace Slag Cement:
This cement has well to moderate resistance to sulphate attack from soil. This cement has some other very desirable qualities of stability details of which follow below under item 3C.
2-D Pozzolana Cement:
This cement has well to moderate resistance to sulphate attack from seawater or soil containing sulphate.
2-E Low Alkali Cement:
This is a variety of ordinary Portland cement in which the total alkali contents of cement has been controlled to remain below 0.6%. With this reduced percentage of alkali contents the danger of alakie of cement attacking the active silica contents of aggregate is eliminated. Generally we do not have active aggregate of this type in Pakistan but on each large scale-concreting project, test of alkali aggregate reaction must be performed to enshore safety of the project. Certain varieties of Chert-stone found in Pakistan contain active Silica and would require low alkali for making concrete.
Low Heat of Hydration Cement:
Normal and Rapid Hardening Cement generate lot of heat during the setting and hardening process so much so that the structure under concreting can crack. This can occur specially while poring large messes of concrete in confine spaces like those of Dam and Bridge pier foundations. In order to avoid this problem cement of low Heat of hydration have been developed some of which are as listed below:
3-A Low Hear of Hydration Cement (type IV of A.S.T.M.)
3-B Portland blast Furnace Slag Cement
3-C Pozzolana Cement
3-D Super Sulphate Cement
3-A Low Hear of Hydration Cement (type IV of A.S.T.M.):
This is cement specially meant for the concreting of structures where large masses of concrete have to be poured at one time. Generally it is specified that heat of hydration on 7 days will not exceed 250Kg. This is achieved by making this cement with larger percentage of di-calcium silicates in its contents than normally presents in OPC. In A.S.T.M this cement is designated as type IV and under BS as LHP. Under German standards its type is LAHORE with symbol as N.W. while the Japanese equivalent is type L.H.P with symbol as M.H.C. The disadvantage of this cement is its slow development of strength and is therefore not used at sited where rapid hardening or other specific qualities are required.
3-B Slag Cement:
This is another variety of low heat cement. Grinding 35% to 65 % of granulated blast furnace slag with ordinary Portland cement clinker produces it. The higher the slag contents, the lower are the 3 and 7 days strengths but better is the resistance to chemical attack. Under German standards as much as 90% slag can be used with type HOZ cement and under Japanese standard up to 70% in the type BSCC. This cement is slower hardening compared to OPC- its strength compared to OPC in ASTM being as follows:
|
OPC
|
B.F SLAG CEMENT
|
3 days strength
|
1,800
|
760
|
7 days strength
|
2,800
|
1,400
|
28 days strength
|
4,000
|
3,000
|
This cement besides being a low heat cement has also the advantage of being medley sulphate resistant although it cannot replace the highly sulphate resistance cement for marine piles and foundations. This cement has excellent resistance to weak organic acids present in the soil and has also the very desirable quality of protecting reinforcement steel better than any other cement.
3-C Pozzolana:
Grinding various proportions of natural pozzolana, tars or volcanic ash with ordinary Portland clinker makes this cement. It is very good cement in the sense that it has good workability properties in addition to having low heat and moderate sulphate resisting properties. It has been used extensively in the 37KM long causeway connecting Dhahran with Bahrain in the gulf. So far in Pakistan we have not been able to locate useful pozzolana deposits, but there are indication that there may be good deposits of this material in the overburden of coal deposits of Sindh.
3-D Super Sulphate Cement:
This is another variety of low heat cement. Its standards exist under B.S but not under A.S.T.M. it is made by grinding about 70-80% B. F. Slag with about 10% gypsum and 1-2 % Portland clinker or lime. This cement is also middy resistant to sulphate attack. It is very finely ground cement and its early strength at 3 day is comparable to OPC although under the BS its 7 days strength is required to be comparable to at least the 3 days strength of OPC. This cement is also good masonry cement due to its good workability but it can be used in RCC and other construction work in the same manner as OPC is used with excellent results.
Cement For Better Protection of Reinforcement against Corrosion:
The basic steps for the prevention of resulting of steel in concrete is to use such cement aggregate and mixing water as are basically free from chlorides, maximum contents of chlorides in concrete being limited to 0.02 % by weight. The following properties in cement are essential for greater protection of steel:
1. Cement to be with minimum percentage of Chlorides says not exceeding 0.01 per cent.
2. Portland Cement preferably having about 6 to 8 per cent Tricalcium Aluminates.
3. Cement made with slag as additive.
If the Tricalcium Aluminates is less than 5 per cent as per ASTM the cement will not have the capacity to neutralize the stray Chloride entering into concrete and thus fail toward off the effects of Chlorides. The properties of slag cement with about 35 percent slag and 60 per cent Portland Clinker are superior to other cement in this respect.
Cement for Better Workability and Wealth E.W. Resistance
These are cement, which are render the corresponding concrete more workable than other normal cement. This quality is necessary where high compatibility and better weather resistance is demanded. Because of greater workability the concrete made from this cement can achieve much higher strength due to lower water cement ratios achievable compared with other cement.
This property is given to the cement by addition of the entraining agents like lime or other plasticisers so that the remix and to place in position. Some of the cement belong to this category are:
Air Entraining Cement:
Under ASTM four different types of cement have been classified as air-entraining version for normal Rapid-hardening and Sulphate Resisting Cement and each concrete thus made is more workable and attains higher weather resisting property compared to their non-air entrained versions.
Blended Hydraulic and Masonry Cement and Grouts:
This cement is basically made for plastering and grouting. Standards have been laid down for this cement both in the British and ASTM specifications. In fact under ASTM there are at least 10 versions of Masonry cement. Some of the standards are for OPC based cement with or without air entraining agents while others are for sulphate resistance and low heat versions. This masonry cement is made by addition of plasticizing materials like lime, ground silica, slag or Pozzolana and air- entraining agents’ etc. Portland Cement clinkers during grinding.
Decorative Cement Oil Well and other Special Purpose Cement:
This cement is basically of properties similar to O.P.C except that it is made from such raw materials, which contain the least amounts of coloring pigments like traces of iron, manganese and chrome. Basically this cement has higher Tricalcium Aluminates in its contents than OPC and therefore subjects to sharp attack by sulphate from any source.
|